The next generation of 3D printers
3D printers are emblematic of what the future of technology could look like. Versatile, flexible and highly adaptable, they promise to produce everything from customised furniture to transplantable organs. Yet the concept of the 3D printer, its place in our imagination, has outstripped its current technical capacity. At the Royal Institute of Technology in Sweden, Professor Frank Niklaus and his research team have set themselves a challenge: to engineer a 3D printer fitted to the modern manufacturing world, capable of producing micro- and nano-structures and, ultimately, superior micro-materials.
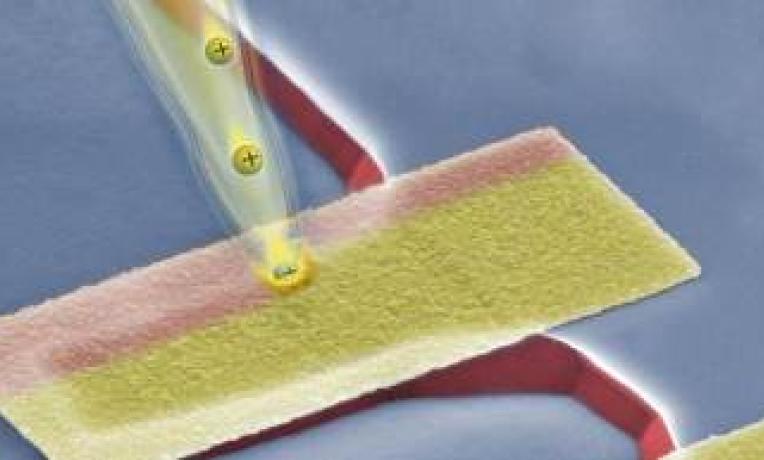
A member of Prof. Niklaus’ team, Dr Andreas Fischer, is presenting their research at the event “New Technologies from the ERC” in Brussels on 4 July. Assessing their preparations for pitching at this event, they comment: “We found the transition from identifying applications in research terms to potential ‘killer’ industrial applications a complex one. We have, however, identified many promising leads for our technology: even in surprising areas such as high-end watch making”.
Scaling up research on micro- and nano-materials
Research into expanding the capabilities of 3D printers was the natural extension of Prof. Niklaus’ ERC Starting grant. His project tackled a systems engineering conundrum: how can materials be manufactured at the micro- and nano-scale when manufacturing systems insist that production scale (and costs) follow an established pattern? Discussing his research, Prof. Niklaus comments: “The development of a suitable 3D printing tool is vital if the research findings are to have a greater impact”. As part of his Starting grant, Prof. Niklaus examined the constrictions operating on silicon micro and nano-fabrication technologies. The ambition was to develop new fabrication processes adapted to the needs of micro- and nano-devices, pave the way for new industrial applications, and increase competitiveness.
With his team, he now explores the burgeoning possibilities of micro- and nano-electromechanical systems (MEMs and NEMs), which are used in applications as diverse as hearing aids’ microphones, automotive safety systems and smartphones. Their wider application is held back by the rigidity of current manufacturing models, which rely on integrated circuit system manufacturing technologies. These technologies demand an operational scale which hinders innovation.
Prof. Niklaus’ contention is that opportunities are being lost in the adherence to the old established way of doing things. Modernised, flexible manufacturing processes would cut costs, and would open out new innovative technological potential: which would no longer be inhibited by the need to think in terms of a factory-sized setup, and factory-scale outputs.
Printing silicon
Prof. Niklaus has established the technical feasibility of printing silicon to the requisite thinness. He explains: “The new technology uses a layer-by-layer process: the 3D patterns are defined in the silicon by using focused ion beam writing, followed by silicon deposits. The structure is built up by repeating these two processes again and again. At the end of the process excess silicon is dissolved using etching.” These findings have implications for both the medical and industrial fields, as well as for photonics, and engineering research more broadly.
This innovative system would not only be a step-change in terms of flexibility: it would be less resource intensive, and as such operate with much reduced overheads. A customised, integrated single tool would allow users to print 3D silicon micro- and nano-structures directly from computer generated designs.
Prof. Niklaus emphasises that the ERC grant has enabled his laboratory to “address more fundamental research questions than would otherwise have been possible.” Not only this: “Funding from the ERC has brought much prestige for the group which motivates us to go even further in the pursuit of high-impact research.” He adds: “The Proof-of-Concept grant is a seed funding which allows researchers to follow through their findings and prepare to meet the market. This support is instrumental in ensuring that excellent ideas are not lost for want of support in the often daunting pre-development stage: the “valley of death” between discovery and its application.”
Ultimately, his goal is to establish the commercial potential of the research findings, and to identify suitable industrial partners.